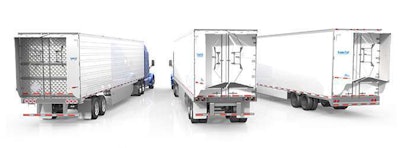
Aerodynamic characteristics around the fifth wheel and the trailer’s rear are difficult to manage. The trailer gap is a necessary open space that allows for full articulation as the rig maneuvers in tight surroundings.
But in aerodynamic terms, that massive gap is a huge drag inducer on the entire vehicle. At highway speeds, as air flows past the tractor heading for the trailer, it encounters a large vacuum area created by the gap’s open space.
The same holds true for the back of a trailer. As air passes around it, a natural vacuum forms behind the vehicle that air seeks to fill.
The result is drag, which leads to aerodynamic inefficiency. Drag makes a vehicle more difficult to move down the road efficiently. The engine must work harder to overcome it, burning more fuel as a consequence.
Smart fleet managers understand the importance of reducing these large areas of turbulence and drag. Fortunately, tractor-trailer aerodynamics have become better understood in recent years, leading to new devices that help smooth airflow past the trailer gap and behind the trailer.
“Until about 2000, tractors and trailers were really manufactured in isolation from each other,” says Kent Smerdon, vice president of international marketing for Aeroserve Technologies, which manufactures and sells Airtab vortex generators. “This concept is changing, with the industry appreciation that a large gap is an aerodynamic and fuel problem area.”
Today’s aerodynamic innovations include high-rise condo – or load-height matching – full fairings and side extenders. “From the trailer side of the equation, rounded front corners and devices such as nose cones have helped with drag reduction efforts,” Smerdon says.
Jeff Grossmann, director of engineering for aerodynamic device manufacturer Stemco, believes that North American truck fleets have learned that closing the tractor-trailer is the easiest way to save fuel and improve fuel economy.
“Just closing the gap a mere five inches – from 50 to 45 inches, for example – offers fleets large and immediate fuel savings,” Grossmann says.
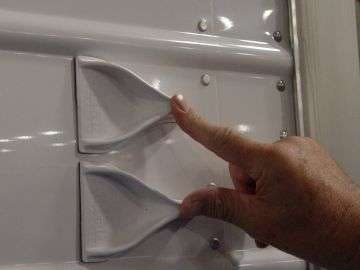
Tackling the total package
Smerdon says that although OEMs have improved their designs for more aerodynamic efficiency, fleet managers should understand that only the separate tractor and trailer have been optimized, not the total package.
“The connection point between these two items is the big variable, and the best gap of all is no gap at all,” he says. “Add-on aerodynamic fairings and side extenders can help reduce the gap, but it still exists and will remain a significant source of drag until a practical way to eliminate it is invented.”
Aeroserve offers vortex generators that attach to strategic points on a tractor to help direct airflow around the gap and decrease unwanted wraparound turbulence and crosswinds. “Vortex generators offer fleets the option of setting their kingpins for optimum axle loading for their loads without any loss of fuel economy,” Smerdon says.
Vortex generators are designed for easy installation and to deliver a cost-effective benefit by fitting only the tractors, and the results sound impressive. Smerdon says the current best-selling vortex generator claims a 2- to 3-percent fuel savings on a fully faired tractor-only installation for a typical dry van gap.
Turning to the trailer’s rear, Grossmann believes trailer skirts and boat tails working in conjunction with one another represent the largest fuel-saving opportunity available to fleets today. Stemco manufactures TrailerTail boat-tail aerodynamic devices.
“Our TrailerTail aerodynamic device smooths airflow past this large low-pressure area and can give fleets up to 9 percent fuel economy boosts at highway speeds,” he says. “The key is to work closely with both your OEM as well as an aerodynamic provider to ensure that you’re running the most aerodynamically clean vehicle possible. Any aerodynamic gain achieved anywhere on a tractor-trailer, no matter how small, is always beneficial.”
The gap battle continues
Another aerodynamic efficiency-solution company that isn’t shying away from the challenges posed by the gap is SmartTruck, which last month introduced its LeadEdge Top Fairing, a new aerodynamic trailer fairing designed to manipulate and manage the disruptive airflow created in the gap between either the cab and trailer or between two tandem trailers.
“This new patent-pending product addresses this problem area of the trailer in a completely new and different way,” says Stephen Ingham Jr., SmartTruck chief executive officer. “LeadEdge creates lift to reduce drag.”
Like other components in Smart Truck’s product portfolio, the LeadEdge is designed to increase long-haul truck fuel efficiency: a 2 percent improvement as a standalone and an incremental improvement in fuel economy when combined with other aerodynamic systems addressing drag in other parts of the trailer.
For tandem operators in particular, the LeadEdge Top Fairing can pay for itself quickly in fuel savings, Ingham says.
“Tandem trailers face a unique aerodynamic challenge,” he says. “They need to ensure than any efficiency components added to trailers do not obstruct or interfere with pup operations. Our LeadEdge was created with that in mind.”
The LeadEdge Fairing was designed and optimized using sophisticated computational fluid dynamics, and SmartTruck says predicted performance metrics were validated subsequently through rigorous coast-down testing. Live tandem fleet testing is expected to be completed in the fourth quarter of 2015.